Our Oil Mill
Our state-of-the-art oilseed mill is the latest innovation at Natural Plant Products. The final phase, completed in October 2023, brought expeller pressing of our meadowfoam and daikon seed crops in-house, mere miles from where the seed is grown. This improves our supply chain, both in terms of transparency and quality control, reduces our carbon footprint, and allows us to be more responsive to customer needs. Learn more about how the mill works and the steps involved in producing high quality seed oils for the personal care industry.
Our Process
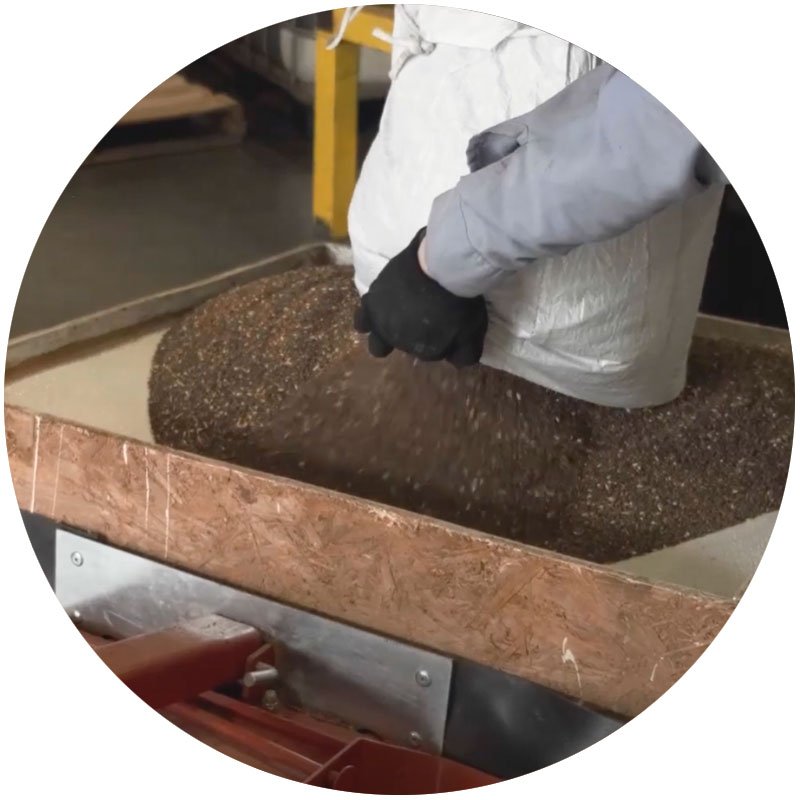
Seed Loading
- The seed enters the system through an aspirator, which uses air and a vibrating plate to remove dust from the seed.
- The dust-laden air is pulled away by a dust filtration fan and exhausted outside the building.
- From there, the seed travels to either our seed bins for storage or day tanks which feed directly into the presses.
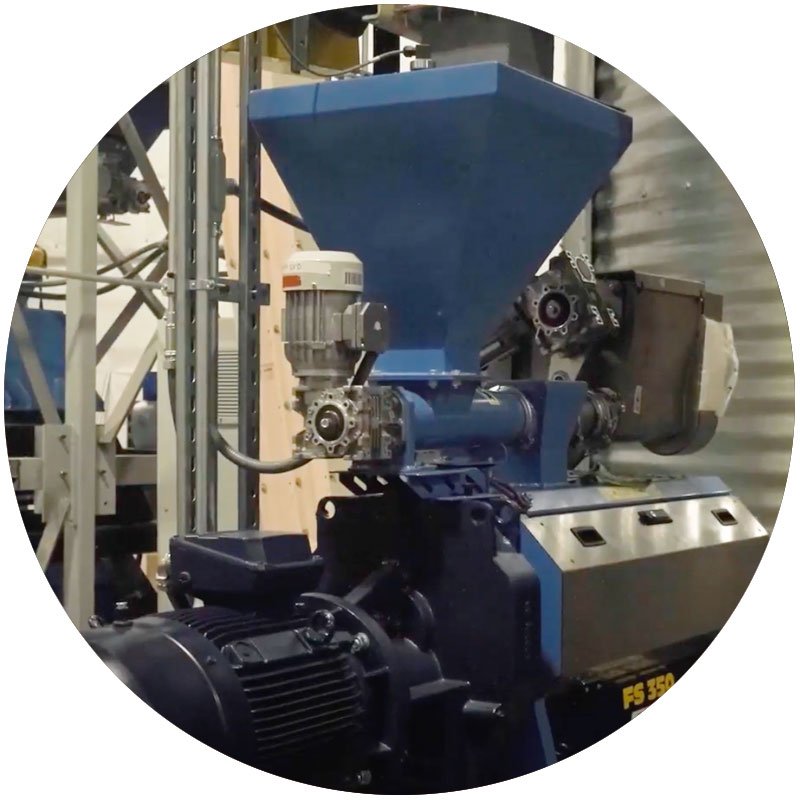
Pressing
- As seed travels from the day tanks to the presses, it is first run through our scale to track throughput and keep a running total of seed processed each day.
- The seed is transferred from the scale into our press hoppers. From there, the seed is fed into the press screw via the dosing screw, which controls the feed rate.
- The press screw compacts the seed, gradually increasing the pressure and crushing the seed under the force of the screw. The oil separates from the seed and is discharged from the bottom and sides, through the segments. The by-product presscake is expelled out of the end of the press.
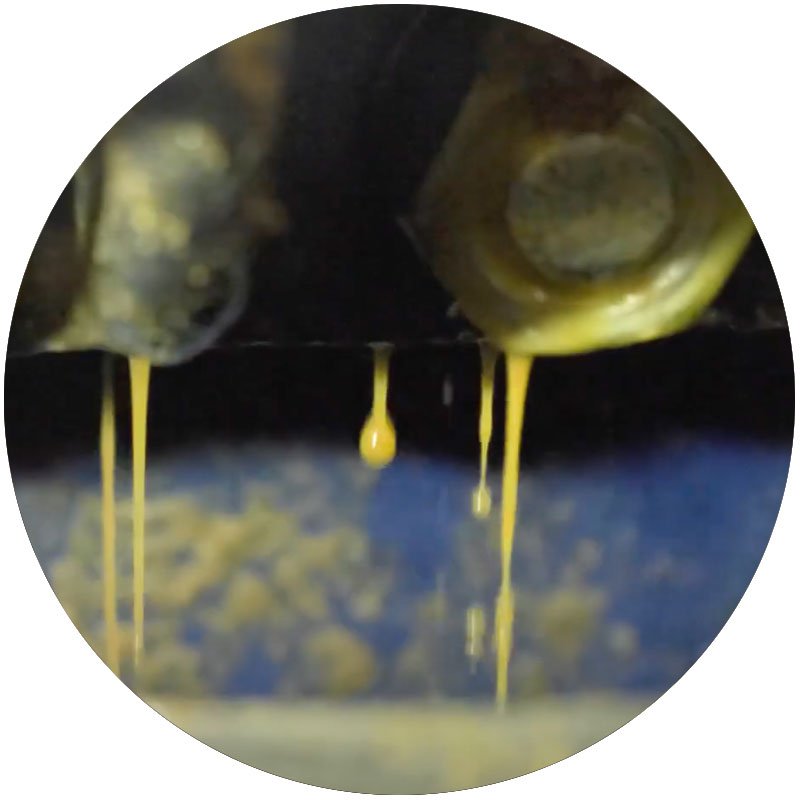
Presscake and Oil Collection
- The oil extracted from the seed and foots (a residual byproduct) is collected in the basin. We then pump out the oil to our crude filtration tank or recirculate the oil in the basin for a good mix before pumping out to the crude tank.
- The foots return is a rake conveyor that sits in the press basin and rakes up the foots via a chain and feeds it back into the screw for re-processing. This allows for a higher oil recovery and oil that is mostly free from particulates, which makes for easy filtering.
- Once the presscake is expelled out of the press, it is collected by a drag conveyor, sent through a cooling conveyor, and transported to our presscake storage tanks.
- When the presscake storage tanks are full, we load it into poly bags or a bulk truck via our presscake loadout elevator.
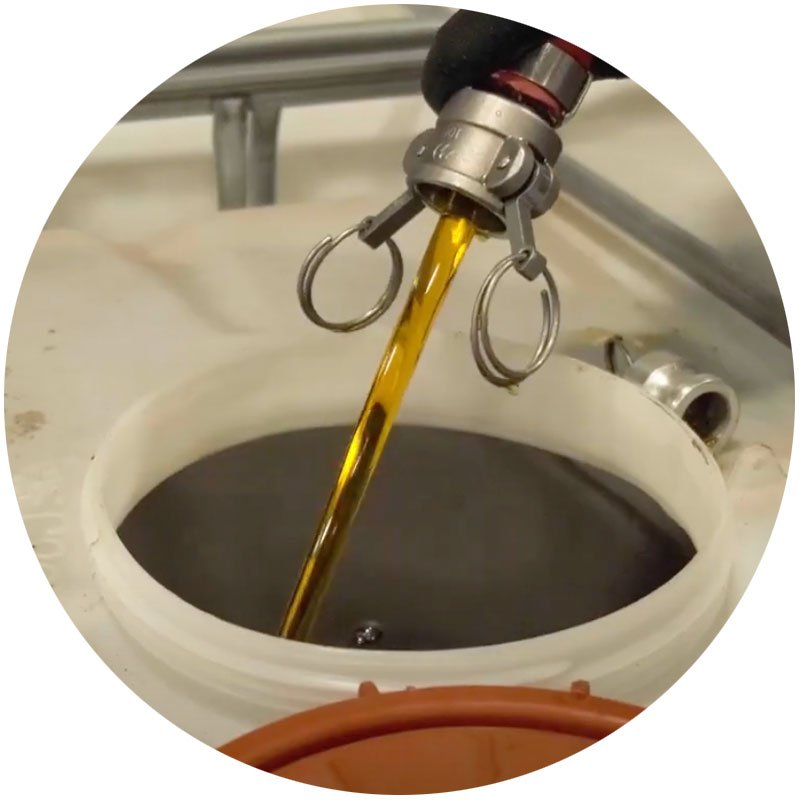
Filtration
- The freshly extracted oil collected in our press basins is pumped out into the crude filtration tank which houses the oil that will be filtered using our Watermark filter press.
- Horizontally-stacked filtration plates catch particulates and fines (foots, but smaller) and keep them trapped between the plates, allowing particulate-free oil to be pumped into our storge containers, ready for shipment to be refined.
- After the press is filled with fines, we pump continuous stream of air through the filter plates to push any residual oil trapped in between the plates back into our oil tank to be used in the next filtration cycle. This also dries out the fines trapped in the filter plates which create a dry filter cake that we can sell to be used as fertilizer.
- Once our crude oil is filtered, it’s ready to be shipped out for refining into the finished product, then sold to manufacturers around the globe for use in a wide range of personal care products.